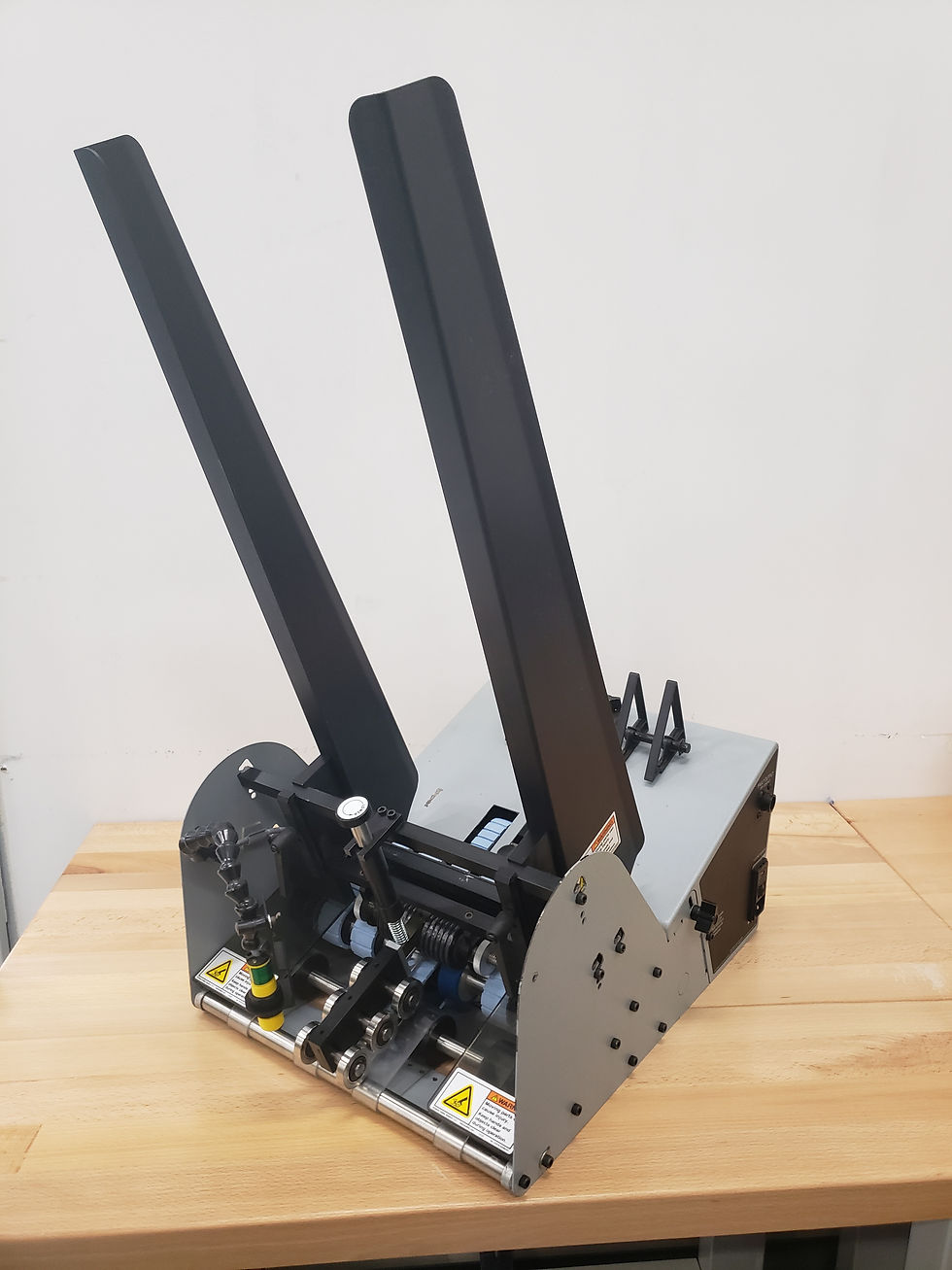
Friction feeders are specialized machines designed to streamline industrial operations. They do this by automating the feeding of individual items into a production or packaging line. These machines rely on frictional forces applied by rollers or belts to separate and feed materials. Materials fed through the friction feeder include paper, cards, labels, or even lightweight plastic and metal parts.
This beginner's guide will teach you everything you need to know about friction feeders from the very basics.
Types of Friction Feeders
Friction feeders can be classified as:
Continuous Feeders
Continuous feeders are made for high-speed production. Productions like Inkjet Printing, Addressing, and Labeling. These feeders ensure seamless and accurate feeding even at high volumes. They handle various paper weights and sizes with ease while offering durability and minimal maintenance. Continuous feeders are available in 12” 14 and 20” widths for flexibility in production volume. They are ideal for feeding envelopes, self mailers, brochures, and more.
Staging / Presentation Feeders
Ideal for swing arm inserters and manual order fulfillment. These feeders minimize jams and errors while handling a variety of products. They are simple to maintain and can be adjusted for different materials. Staging feeders are commonly used for brochures, postcards, and envelopes. They are a reliable choice for businesses seeking cost-effective and efficient feeding systems.
On-Demand Feeders
These are highly flexible and precise feeders. They can handle various materials and sizes with ease while switching tasks quickly without much setup. Equipped with options like misfeed detection and external integration, they are highly efficient and accurate. On-demand feeders are suitable for magazines, envelopes, tags, and more. They are indispensable in work environments requiring adaptability and reliability.
Batch Counting Feeders
Engineered for precision, these feeders count and stack materials for processes like banding or shrink wrapping. They eliminate manual errors, integrate seamlessly into packaging lines, and improve productivity. Widely used in industries such as pharmaceuticals and contract packaging. They are perfect for inserting instructions or promotional materials with unmatched efficiency.
Click here for a more detailed explanation on these friction feeder types.
How Do Friction Feeders Work?
Friction feeders rely on the interaction between machine components and a stack of materials. This interaction brings about the separation of materials from a stack and their feeding into the next stage of a process.
The stack of materials stays together due to the friction between them. Feeding can only occur when the feeder belts create enough friction to overcome this friction. This process is assisted by a gating mechanism. Some gating mechanisms are static while others have powered rollers.
The process of feeding is summarized below.
Loading the Material: Items to be fed, such as envelopes, sheets, or cartons, are stacked vertically in a hopper or tray at the entry point of the machine.
Separation Mechanism: The feeder uses a series of friction rollers or belts. They grip and separate the bottom-most item from the stack. You can adjust the friction level to allow for handling a wide variety of product types, sizes, and textures.
Dispensing: Once separated, the item is fed into the production line at a controlled speed. This step ensures synchronized feeding which reduces errors in downstream processes.
Automation and Control: Modern friction feeders are equipped with sensors and programmable controls. These systems monitor operations in real time, adjust for jams, and optimize feed rates.
Applications of Friction Feeders
Friction feeders are versatile and widely used across different industries. Here are some key applications:
Packaging Industry: They are employed to insert promotional materials, leaflets, or instructional booklets into product packaging.
Printing and Mailing: Printing companies use friction feeders to feed sheets, labels, and envelopes into printers or binders. Similarly, mailing houses rely on them to process large volumes of mail efficiently.
Pharmaceuticals: In the healthcare sector, friction feeders ensure the precise insertion of dosage instructions or safety leaflets into medicine packaging.
Food and Beverage: They handle the placement of coupons, stickers, or promotional items in packaged goods.
E-commerce and Retail: Friction feeders streamline the inclusion of invoices, return labels, and promotional materials in online shopping packages.
Material Requirements for feeding
Friction feeders generally feed flat materials. However, not all flat materials can be fed due to some factors like texture and thickness. When the materials have a rough texture, it can lead to the generation of static between the stack. This causes the materials to stick together, making it hard to separate during feeding. As for the thickness, the material should be a bit rigid but not too hard. It should be able to bend easily but not to be too flimsy. Flimsy materials get stuck during feeding as they curl up and get bent. This causes jams in the moving parts.
The best thing to do is to check for material specifications when you buy a feeder. Ensure to only feed compatible materials to avoid jams which may lead to breakdown.
Benefits of Using Friction Feeders
The benefits of using friction feeders are numerous. Some of the core benefits include:
Efficiency: Friction feeders provide an easy and efficient way of performing feeding tasks. You can automate repetitive feeding tasks and reduce manual labor. This generally boosts productivity by speeding up production lines.
Precision: If there is one thing a friction feeder makes sure of, it is precision. It ensures accurate placement of items, minimizing errors and rework. This saves you a lot of money from human errors.
Cost-Effectiveness:Companies can save a lot from using friction feeders. They reduce operational costs by optimizing labor and material use
Versatility: Handles a variety of materials, from paper to lightweight plastics and metals. Some feeders are built specifically for a particular product while some can handle different materials.
Adaptability: Modern feeders include adjustable settings for different material sizes, shapes, and thicknesses. All you have to do is adjust the settings and you are good to go.
Limitations of a Friction Feeder
While friction feeders are highly efficient, they come with certain limitations:
Material Compatibility: Items that are sticky, extremely slippery, or fragile may not work well with friction feeders. This limits the type of materials you can feed using a friction feeder.
Maintenance Needs: Although the maintenance can be minimal, regular cleaning and inspection of rollers and belts are necessary to prevent wear and maintain performance.
Setup Complexity: Once properly trained, any operator can easily change products and operate friction feeders.
Initial Cost: High-quality friction feeders may require a significant upfront investment. Although the long-term benefits cancel out this cost, you still need enough capital for the purchase.
Choosing the Right Friction Feeder
Consider the following factors when choosing a friction feeder:
Material Specifications: Ensure compatibility with the thickness, texture, and weight of your materials.
Production Speed: Match the machine's speed to your production line requirements.
Automation Features: Look for feeders with advanced sensors and programmable settings for optimal performance.
Durability and Maintenance: Choose machines made from quality materials that require minimal maintenance.
Budget: Consider your pocket and balance initial costs with long-term benefits.
Conclusion
Friction feeders play a significant role in the modern manufacturing and packaging industry. Their ability to automate the feeding of materials ensures precision, speed, and cost-efficiency. This makes them indispensable in industries ranging from packaging to pharmaceuticals.
Comentarios